At OGE, a new pipeline does not necessarily take the shortest route but the most environmentally compatible one. The primary goal is to minimise the impact on nature and the environment and to preserve the landscape. The Etzel-to-Wardenburg pipeline crosses two sensitive areas: The Bloher Wold nature reserve in Oldenburg and Wehnen, which is bordered by a motorway and a railway line, and the coastal canal in Nord- and Südmoslesfehn in Wardenburg. At these two sites, OGE's experts use a sophisticated technique known as 'microtunnelling' to protect the Bloher Wold reserve and the coastal canal.
Microtunnelling is a pipe laying technique used in sensitive areas of a pipeline route. In contrast to open-trench methods used for large parts of a corridor, this trenchless technique involves the use of hydraulic jacks to push prefabricated pipes through the ground. So instead of digging a trench, the OGE experts excavate a small tunnel under the Bloher Wold for around 660 metres and the coastal canal for a good 460 metres. The tunnel built for the Etzel-to-Wardenburg pipeline has a diameter of two metres.
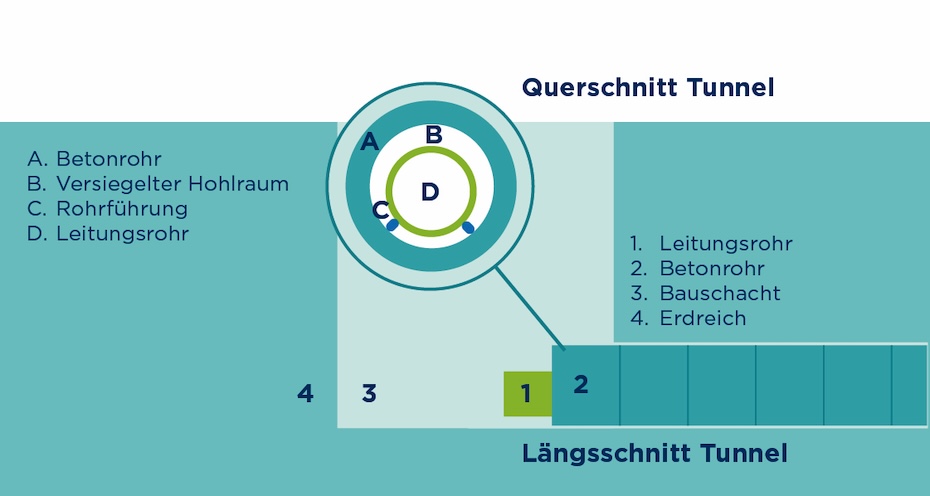
The procedure
At Bloher Wold and the coastal canal, the contractor first excavated a launch shaft and a reception shaft six to eight metres deep and then lowered the microtunnel machine with its drill head into the pit. From the launch shaft the machine works its way through the ground to the reception shaft, with the drill head (mix shield/cutting wheel) crushing the soil. The spoil is removed by means of a water/bentonite fluid which is then pumped to a separation plant for separation into its fractions (water, bentonite, spoil). Once separated from the spoil in the separation tank, the bentonite is piped back to drill head. This principle provides a closed loop for the removal of rock, soil and sediments. Behind the drilling machine, the contractor lowers concrete pipes into the shaft one by one, which are then jacked forward. These concrete pipes are four metres long and weigh two and a half tonnes and form the casing for the 18-metre-long and 12.5 tonne pipes.
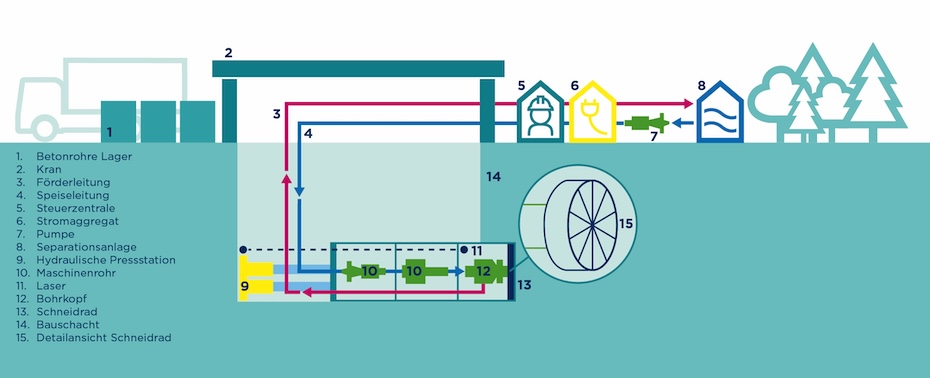
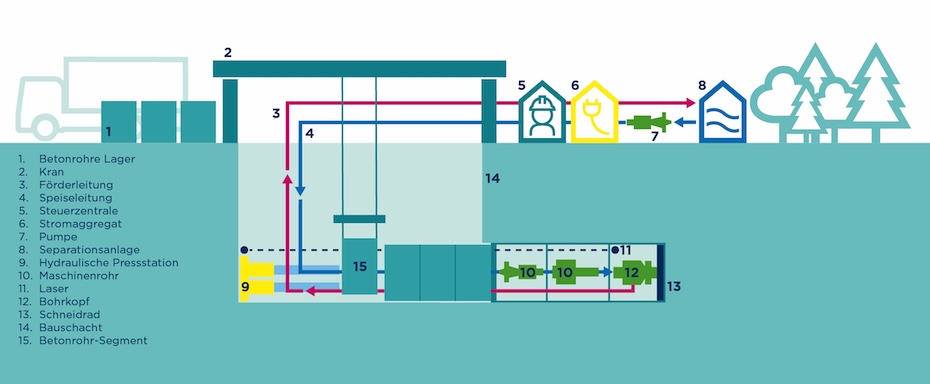
After completion of the tunnel, the actual pipeline is introduced into the concrete casing. The line pipes, which have a special corrosion protection coating, are welded together by specialist welders over the entire length of the tunnel, i.e. 460 and 660 metres. The annular space between the pipes and the concrete casing of the tunnel is then sealed and the two shafts are backfilled. Above ground, recultivation then commences. Once this work is complete, the tunnel and the pipeline, which are now located at a depth of around six to fifteen metres below the Bloher Wold and the coastal canal, will no longer be visible.
"Microtunnelling is a complex and expensive process but it allows us to complete projects on time even if the route includes technically challenging sections,"
explains project manager Franz-Josef Kißing. The use of microtunnelling is nothing new at OGE. The method has proven its worth on numerous projects at a number of technically challenging crossings along the route. However, it is always exciting to follow the progress of the powerful drilling machine and then see the finished underground structure. With the Etzel-to-Wardenburg section of the pipeline scheduled for commissioning the by the end of 2025, the tunnel is set to be completed by early 2025.